Schlüsselrolle für die Spindel
Ein Entwicklungs-Schwerpunkt von ISCAR
Die Hochgeschwindigkeits-Bearbeitung (HSM) unterschiedlicher Materialien erfordert leistungsstarke Werkzeugmaschinen. Eine besondere Rolle spielt dabei eine innovative Spindeltechnologie, auf die ISCAR einen Entwicklungs-Schwerpunkt legt. Nur eine optimale Abstimmung zwischen Werkzeughalter, Schneidwerkzeug und Spindel sorgt für hohe Prozesssicherheit, führt zu den gewünschten Bearbeitungsergebnissen und minimiert die Gefahr für Mensch und Maschine.
Um eine Spindel prozesssicher mit hoher Drehzahl zu betreiben, ist eine exakte Balance zwischen der bereitgestellten Drehzahl und dem Drehmoment erforderlich. Die Leistung der Spindel hängt unterdessen von verschiedenen Faktoren ab wie dem Konstruktionskonzept des Lagersystems, der Dichtungskomponenten und der Auslegung des Werkzeughalters.
Eine wichtige Rolle übernimmt der in die Spindel montierte Werkzeughalter. Eine schlechte Performance der aus Werkzeug und Halter bestehenden kleinen Baugruppe kann die Funktion der Spindel erheblich beeinträchtigen. Deswegen muss der Halter bei der Hochgeschwindigkeits-Bearbeitung präzise, zuverlässig und sicher montiert sein.
Fliehkräfte wachsen exponentiell
Bei der HSM-Bearbeitung wachsen die Fliehkräfte exponentiell an und belasten das Schneidwerkzeug erheblich. Dies beeinflusst auch dessen Lebensdauer. Beim Fräsen mit Wendeschneidplatten können hohe Fliehkräfte beispielsweise dazu führen, dass die Klemmschrauben der Schneidplatten brechen und sich die Platten lösen. Dadurch entstehende Bruchstücke können nicht nur die Maschine und das bearbeitende Werkstück beschädigen, sondern auch den Bediener gefährden. „Wir als Hersteller legen die Schneidwerkzeuge konstruktiv und technologisch so aus, dass deren Prozesssicherheit gegeben ist. Bei Wendeplatten-Fräsern sollte der Fokus auf der sicheren Plattenfixierung und einem robusten Fräskörper liegen“, sagt Erich Timons, CTO der ISCAR Germany GmbH.
Die Klemmschraube ist die kleinste Komponente eines Hochgeschwindigkeits-Wendeplattenfräsers. Sie hat jedoch einen großen Einfluss auf die Zuverlässigkeit eines Systems. Mit einem Drehmomentschlüssel kontrolliert der Anwender die Kraft beim Anziehen der Klemmschraube. Dies reicht jedoch nicht aus. Um die Belastung zu minimieren, ist auch ein spezielles Design erforderlich.
Schnitttiefen bis 22 Millimeter
ISCAR hat sich diesen Herausforderungen gestellt und führt eine Reihe innovativer Werkzeuge für dieses Einsatzgebiet im Portfolio. Für effizientes Fräsen von Aluminium bei hohen Geschwindigkeiten wurde beispielsweise der Fräser HSM90S FAL-22 entwickelt. Bestückt mit großen Wendeschneidplatten, sind Schnitttiefen bis 22 Millimeter möglich. Die formschlüssige Absicherung der HSM90S-Wendeschneidplatte im Plattensitz führt zu einer prozesssicheren Bearbeitung und langen Standzeiten bei sehr hohen Drehzahlen. Das Design der Werkzeuge verhindert den bei starken Fliehkräften drohenden Versatz der Schneidplatte. Die Konstruktion erlaubt Fräsen mit einer Drehzahl bis zu 31.000 Umdrehungen in der Minute.
Um Fliehkräfte zu reduzieren, sollte ein Fräskörper feinstgewuchtet sein. Die Wuchtgüten von Werkzeugen sind in internationalen und nationalen Standards und Normen festgelegt. Zudem ist es bei der Konstruktion von HSM-Wendeplattenfräsern mittels CAD/CAM wichtig, dass die Massenverteilung des Fräskörpers achsensymmetrisch verläuft. „Da sich dieses Gleichgewicht in der Konstruktionsphase auf ein virtuelles Objekt bezieht, ersetzt es das physische Auswuchten eines realen Fräskörpers nicht. Aber es kann die Massenunwucht eines künftigen Produkts erheblich verringern und damit das Auswuchten am realen Werkzeug erleichtern“, schildert Erich Timons.
Um die Verschleißfestigkeit zu erhöhen, sind Fräskörper, insbesondere die Plattensitz-Oberfläche, so hart wie möglich gestaltet. Doch dies birgt auch Risiken: Je härter das Werkzeug ist, desto schneller kann es brechen. Daher ist bei der Konstruktion effektiver HSM-Werkzeuglösungen ein optimales Verhältnis zwischen Festigkeit und Verschleiß wichtig.
Starker Auftritt für VHM-Fräser
Neben Wendeplatten-Fräsern spielt auch eine andere Variante ihre Stärken aus: Vollhartmetall (VHM)-Werkzeuge sind im Vergleich präziser und axial symmetrischer. Sie haben in der Regel einen geringeren Durchmesser, benötigen aber bei gleicher Schnittgeschwindigkeit höhere Drehzahlen. Obwohl Keramik als Werkzeugmaterial für die HSM-Bearbeitung von hoch hitzebeständigen Superlegierungen Terrain erobert hat, sind VHM-Werkzeuge in der Hochgeschwindigkeits-Bearbeitung weit verbreitet.
Die Auswahl eines geeigneten VHM-Werkzeugs, insbesondere von Fräsern, ist anspruchsvoll. In der Regel ist das Verhältnis der Auskragung zum Durchmesser bei VHM-Schaftfräsern größer als bei Wendeplattenwerkzeugen. Dazu kommt eine spezielle Spannutform, die den Werkzeug-Querschnitt beeinflusst. Dies führt dazu, dass die Konstrukteure ein besonderes Augenmerk auf die Vibrationsbeständigkeit eines VHM-Schaftfräsers legen müssen. Um diese zu verbessern, entstehen oft eine ungleiche Zahnteilung und unterschiedliche Spiralwinkel der Spannut. Dies verstößt jedoch gegen den Grundsatz der axialen Symmetrie und kann das Bearbeitungsergebnis negativ beeinflussen. Ein Lösungsansatz besteht aus einem speziellen, intelligenten Design in Kombination mit ausgeklügelten Kompromissen.
Ein effizientes, vibrationsstabiles Werkzeug ist die halbe Miete bei der Hochgeschwindigkeits-Bearbeitung. Doch auch der auf der Spindel montierte Werkzeughalter muss hierfür geeignet sein. Bei HSM-Prozessen können die dynamischen Eigenschaften des Werkzeugs aus Sicht von ISCAR nicht getrennt vom Halter betrachtet werden. „Das Auswuchten des Werkzeugs sollte beispielsweise zusammen mit dem Werkzeughalter erfolgen. Dies ist der einzige Weg, um präzise und sichere Ergebnisse zu erhalten“, sagt Erich Timons
Spindeln mit maximaler Effizienz
Hochgeschwindigkeitsspindeln arbeiten heute dank spezieller Schneidwerkzeuge und Werkzeughalter mit maximaler Effizienz. ISCAR bietet Anwendern zudem die Möglichkeit, bereits in der Konstruktionsphase den Grundstein für eine effiziente Werkzeuglösung zu legen. Moderne CAD/CAM-Systeme erlauben es, das dynamische Verhalten von Werkzeug, Halter und Spindel auf Grundlage von 3D-Modellen abzuschätzen. Um dieses Potenzial weiter auszuschöpfen, hat ISCAR seinen elektronischen Auftritt in den vergangenen Jahren deutlich ausgebaut. Anwender finden im E-Katalog des Unternehmens (www.iscar.com/eCatalog) zahlreiche Möglichkeiten, digitale Zwillinge für Montage-Optionen zu erstellen und damit spürbar mehr Planungssicherheit zu erreichen.
 
 
 
 
Um eine Spindel prozesssicher mit hoher Drehzahl zu betreiben, ist eine exakte Balance zwischen der bereitgestellten Drehzahl und dem Drehmoment erforderlich. Die Leistung der Spindel hängt unterdessen von verschiedenen Faktoren ab wie dem Konstruktionskonzept des Lagersystems, der Dichtungskomponenten und der Auslegung des Werkzeughalters.
Eine wichtige Rolle übernimmt der in die Spindel montierte Werkzeughalter. Eine schlechte Performance der aus Werkzeug und Halter bestehenden kleinen Baugruppe kann die Funktion der Spindel erheblich beeinträchtigen. Deswegen muss der Halter bei der Hochgeschwindigkeits-Bearbeitung präzise, zuverlässig und sicher montiert sein.
Fliehkräfte wachsen exponentiell
Bei der HSM-Bearbeitung wachsen die Fliehkräfte exponentiell an und belasten das Schneidwerkzeug erheblich. Dies beeinflusst auch dessen Lebensdauer. Beim Fräsen mit Wendeschneidplatten können hohe Fliehkräfte beispielsweise dazu führen, dass die Klemmschrauben der Schneidplatten brechen und sich die Platten lösen. Dadurch entstehende Bruchstücke können nicht nur die Maschine und das bearbeitende Werkstück beschädigen, sondern auch den Bediener gefährden. „Wir als Hersteller legen die Schneidwerkzeuge konstruktiv und technologisch so aus, dass deren Prozesssicherheit gegeben ist. Bei Wendeplatten-Fräsern sollte der Fokus auf der sicheren Plattenfixierung und einem robusten Fräskörper liegen“, sagt Erich Timons, CTO der ISCAR Germany GmbH.
Die Klemmschraube ist die kleinste Komponente eines Hochgeschwindigkeits-Wendeplattenfräsers. Sie hat jedoch einen großen Einfluss auf die Zuverlässigkeit eines Systems. Mit einem Drehmomentschlüssel kontrolliert der Anwender die Kraft beim Anziehen der Klemmschraube. Dies reicht jedoch nicht aus. Um die Belastung zu minimieren, ist auch ein spezielles Design erforderlich.
Schnitttiefen bis 22 Millimeter
ISCAR hat sich diesen Herausforderungen gestellt und führt eine Reihe innovativer Werkzeuge für dieses Einsatzgebiet im Portfolio. Für effizientes Fräsen von Aluminium bei hohen Geschwindigkeiten wurde beispielsweise der Fräser HSM90S FAL-22 entwickelt. Bestückt mit großen Wendeschneidplatten, sind Schnitttiefen bis 22 Millimeter möglich. Die formschlüssige Absicherung der HSM90S-Wendeschneidplatte im Plattensitz führt zu einer prozesssicheren Bearbeitung und langen Standzeiten bei sehr hohen Drehzahlen. Das Design der Werkzeuge verhindert den bei starken Fliehkräften drohenden Versatz der Schneidplatte. Die Konstruktion erlaubt Fräsen mit einer Drehzahl bis zu 31.000 Umdrehungen in der Minute.
Um Fliehkräfte zu reduzieren, sollte ein Fräskörper feinstgewuchtet sein. Die Wuchtgüten von Werkzeugen sind in internationalen und nationalen Standards und Normen festgelegt. Zudem ist es bei der Konstruktion von HSM-Wendeplattenfräsern mittels CAD/CAM wichtig, dass die Massenverteilung des Fräskörpers achsensymmetrisch verläuft. „Da sich dieses Gleichgewicht in der Konstruktionsphase auf ein virtuelles Objekt bezieht, ersetzt es das physische Auswuchten eines realen Fräskörpers nicht. Aber es kann die Massenunwucht eines künftigen Produkts erheblich verringern und damit das Auswuchten am realen Werkzeug erleichtern“, schildert Erich Timons.
Um die Verschleißfestigkeit zu erhöhen, sind Fräskörper, insbesondere die Plattensitz-Oberfläche, so hart wie möglich gestaltet. Doch dies birgt auch Risiken: Je härter das Werkzeug ist, desto schneller kann es brechen. Daher ist bei der Konstruktion effektiver HSM-Werkzeuglösungen ein optimales Verhältnis zwischen Festigkeit und Verschleiß wichtig.
Starker Auftritt für VHM-Fräser
Neben Wendeplatten-Fräsern spielt auch eine andere Variante ihre Stärken aus: Vollhartmetall (VHM)-Werkzeuge sind im Vergleich präziser und axial symmetrischer. Sie haben in der Regel einen geringeren Durchmesser, benötigen aber bei gleicher Schnittgeschwindigkeit höhere Drehzahlen. Obwohl Keramik als Werkzeugmaterial für die HSM-Bearbeitung von hoch hitzebeständigen Superlegierungen Terrain erobert hat, sind VHM-Werkzeuge in der Hochgeschwindigkeits-Bearbeitung weit verbreitet.
Die Auswahl eines geeigneten VHM-Werkzeugs, insbesondere von Fräsern, ist anspruchsvoll. In der Regel ist das Verhältnis der Auskragung zum Durchmesser bei VHM-Schaftfräsern größer als bei Wendeplattenwerkzeugen. Dazu kommt eine spezielle Spannutform, die den Werkzeug-Querschnitt beeinflusst. Dies führt dazu, dass die Konstrukteure ein besonderes Augenmerk auf die Vibrationsbeständigkeit eines VHM-Schaftfräsers legen müssen. Um diese zu verbessern, entstehen oft eine ungleiche Zahnteilung und unterschiedliche Spiralwinkel der Spannut. Dies verstößt jedoch gegen den Grundsatz der axialen Symmetrie und kann das Bearbeitungsergebnis negativ beeinflussen. Ein Lösungsansatz besteht aus einem speziellen, intelligenten Design in Kombination mit ausgeklügelten Kompromissen.
Ein effizientes, vibrationsstabiles Werkzeug ist die halbe Miete bei der Hochgeschwindigkeits-Bearbeitung. Doch auch der auf der Spindel montierte Werkzeughalter muss hierfür geeignet sein. Bei HSM-Prozessen können die dynamischen Eigenschaften des Werkzeugs aus Sicht von ISCAR nicht getrennt vom Halter betrachtet werden. „Das Auswuchten des Werkzeugs sollte beispielsweise zusammen mit dem Werkzeughalter erfolgen. Dies ist der einzige Weg, um präzise und sichere Ergebnisse zu erhalten“, sagt Erich Timons
Spindeln mit maximaler Effizienz
Hochgeschwindigkeitsspindeln arbeiten heute dank spezieller Schneidwerkzeuge und Werkzeughalter mit maximaler Effizienz. ISCAR bietet Anwendern zudem die Möglichkeit, bereits in der Konstruktionsphase den Grundstein für eine effiziente Werkzeuglösung zu legen. Moderne CAD/CAM-Systeme erlauben es, das dynamische Verhalten von Werkzeug, Halter und Spindel auf Grundlage von 3D-Modellen abzuschätzen. Um dieses Potenzial weiter auszuschöpfen, hat ISCAR seinen elektronischen Auftritt in den vergangenen Jahren deutlich ausgebaut. Anwender finden im E-Katalog des Unternehmens (www.iscar.com/eCatalog) zahlreiche Möglichkeiten, digitale Zwillinge für Montage-Optionen zu erstellen und damit spürbar mehr Planungssicherheit zu erreichen.
 
 
 
 
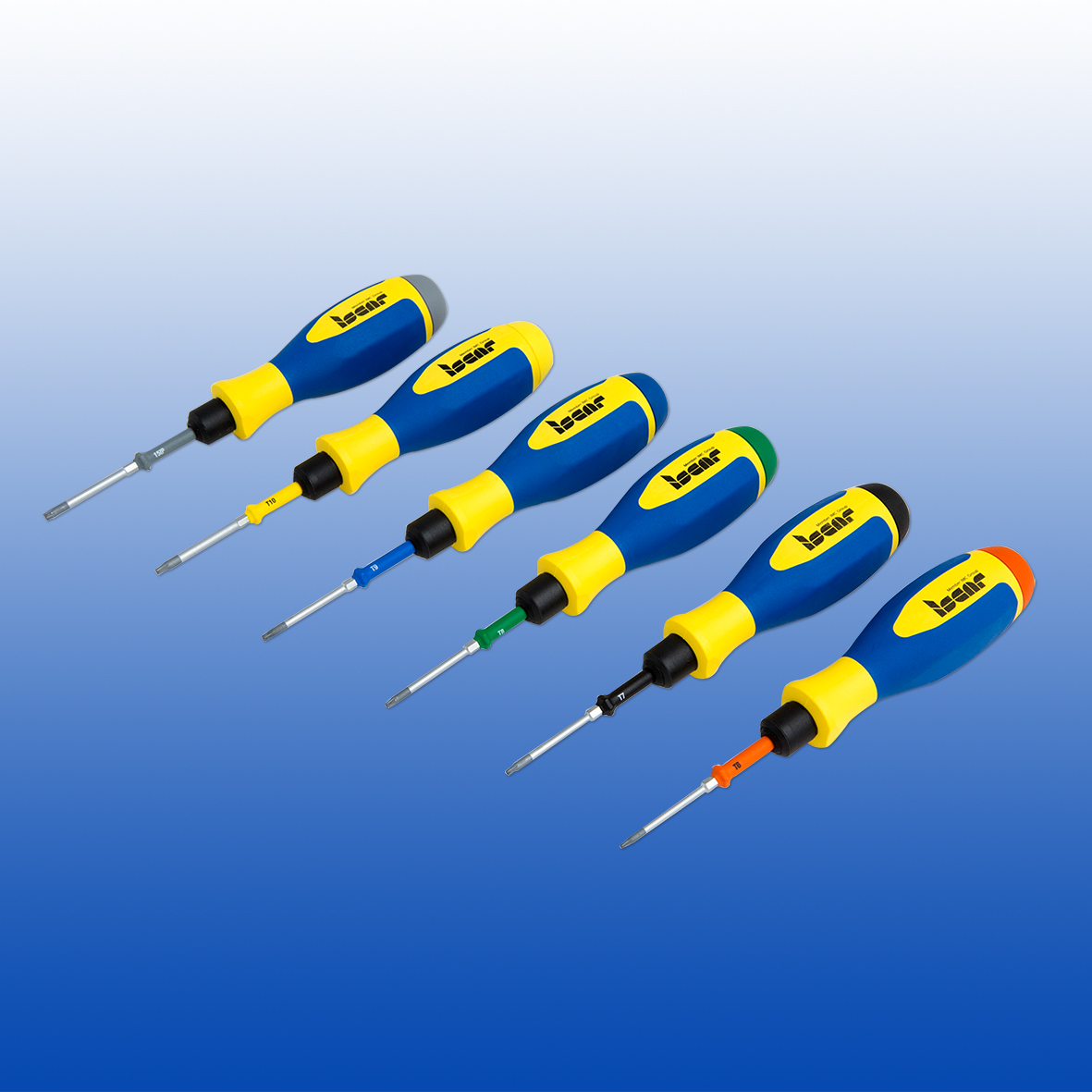
[Bild 1]Modulare, eingestellte Drehmomentschlüssel fixieren Wendeschneidplatten effektiv.
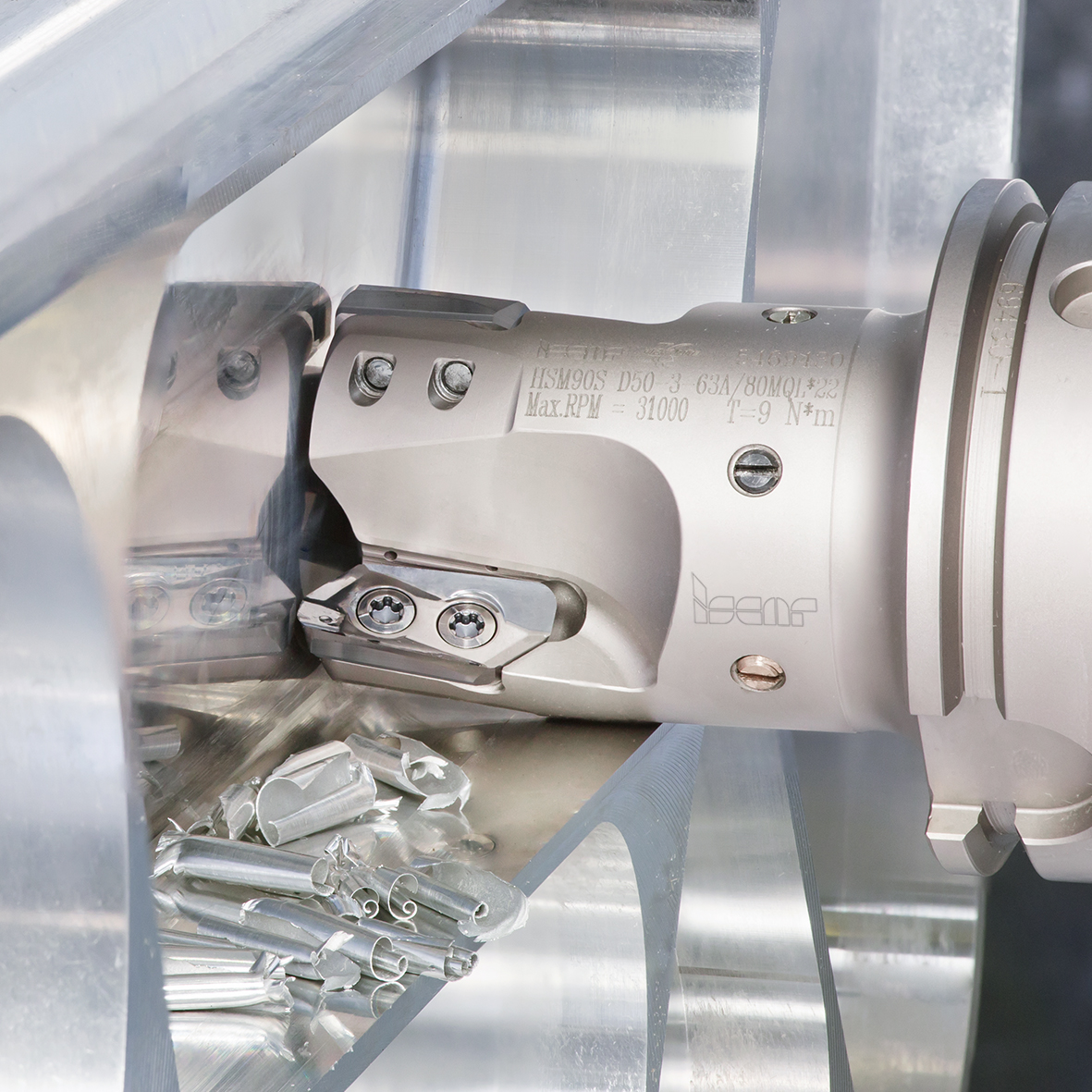
Bild 2]Die robuste Konstruktion von 90-Grad-Wendeschneidplatten-Fräsern ermöglicht das effiziente Bearbeiten von Flugzeugteilen aus Aluminium bei hohen Drehzahlen. Das erforderliche Anzugsdrehmoment für eine Wendeplatten-Klemmschraube und die maximale Drehzahl sind wichtige Parameter.
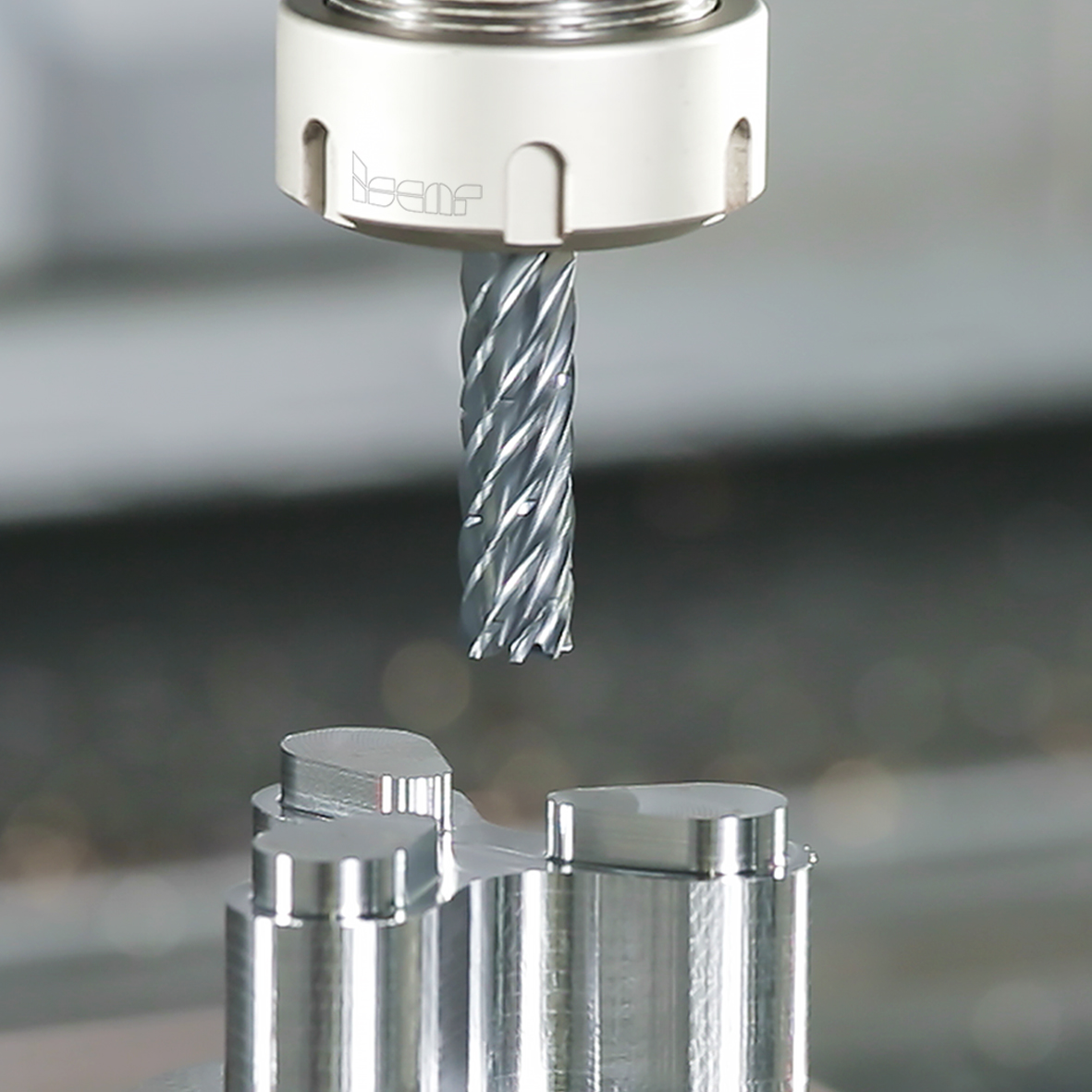
Bild 3]Der siebenschneidige Vollhartmetall-Schaftfräser von ISCAR für die HSM-Bearbeitung verfügt über unterschiedliche Spiralwinkel, ungleiche Teilung sowie Spanteiler an den Schneidkanten.